Mineral oil defoamer have good ability to suppress bubbles, which has been widely used and verified in many industrial fields. The following is an analysis of mineral oil defoamer:
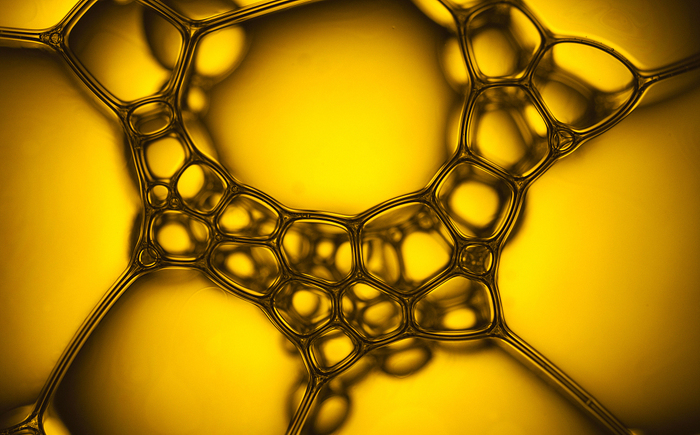
Chemical composition
Main ingredients: Mineral oil defoamer are mainly composed of oily carriers such as mineral oil, vegetable oil, and white oil, which are usually insoluble in the foaming medium.
Auxiliary ingredients: In order to improve the performance of the defoamer, wax (such as ethylene bis stearamide EBS), hydrophobic silica and other ingredients, as well as surfactants may be added to improve emulsification and diffusibility.
Mechanism of action
Reducing surface tension: Mineral oil can destroy the integrity of the liquid film of the foam due to its incompatibility with water, thereby effectively eliminating the foam.
Flowability destruction: When the foam tries to restore the liquid film, it cannot return to its original state due to the presence of mineral oil, resulting in foam rupture.
Preventing the formation of new foam: Mineral oil defoamer form a barrier at the gas-liquid interface to prevent the aggregation of surfactants that stabilize the foam, thereby inhibiting the generation of new foam.
Application areas
Textile processing: In the textile industry, mineral oil defoamer can improve production efficiency and product quality.
Chemical and coatings: As a substitute for surfactants and additives, they are used to improve production efficiency and product quality.
Water treatment and pulp processing: In water treatment and pulp processing, they effectively eliminate foam and maintain the normal operation of the production process.
Food industry: Ensure food quality and taste, suitable for products with strict requirements on color and quality.
Performance characteristics
Low surface tension: The composition of mineral oil gives it very low surface tension, which helps to break bubbles quickly.
Strong environmental adaptability: It can maintain good results in both acidic and alkaline environments, and has good heat resistance.
Does not affect the foaming system: It will not change the basic properties of the foaming system and is suitable for a variety of industrial environments.