Paint defoamer can reduce or eliminate the foam of the coating system kind. It is not possible to eliminate all foam in water-based coating systems but it can be done to control foam generation because coating defoamer can make the film dry without bubbles and without pinhole surface defects.
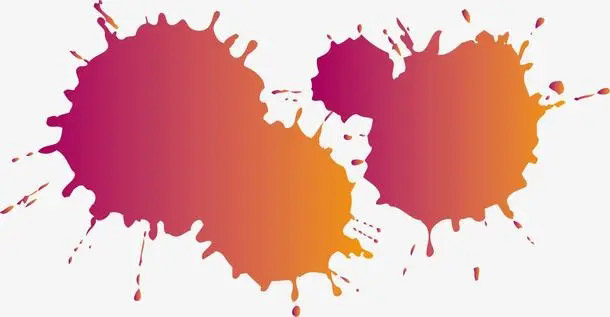
Principle of paint defoamer
Coating defoamer has a good effect on defoaming in the coating system and can maintain the defoaming ability at room temperature and in a heated environment. However, they are not compatible with the foam system and can contribute to foam generation. The coating defoamer in the foaming system has good dispersion. The working principle is to reduce the surface tension of the liquid around the foam so that the small foam will gather into a large foam and eventually make the foam burst.
Influencing factors of coating defoamer
1. Surface tension
Paint surface tension has a greater impact on the defoamer. The surface tension of the defoamer should be lower than the surface tension of the coating or it will not be able to have the effect of defoaming and foam inhibition. The surface tension of the coating is a variable factor, so the choice of defoamer should be constant surface tension and then the surface tension change factor into account.
2. The influence of other additives
Most of the surfactants used in coatings tend to be functionally incompatible with defoamers. Especially emulsifiers, wetting and dispersing agents, leveling agent, and thickening agents will have an effect on the effect of defoamer. So when adding various additives must pay attention to the relationship between different additives to choose a good balance.
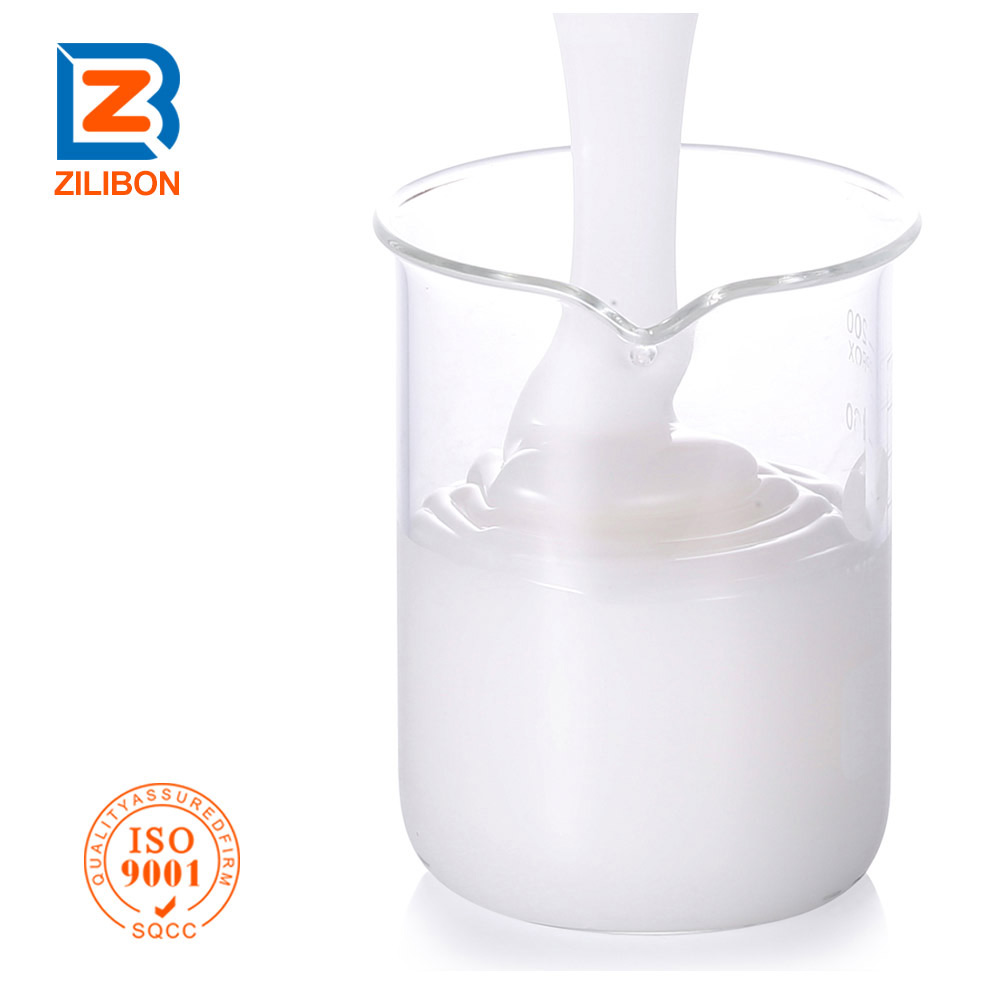
3. Baking temperature
Coating at room temperature into the high-temperature baking viscosity will decline bubbles to appear on the surface However, due to the evaporation of the solvent, the curing of the coating and the increase in surface viscosity will make the foam stable and stay on the surface to produce shrinkage and pinholes. Therefore, the baking temperature, the speed of solidification, and the rate of solvent evaporation also have an effect on the effect of the defoamer.
4. Solid content of paint, viscosity, and elasticity
High solids thick coating film, high viscosity, and high elasticity coatings are very difficult to defoam. In these coatings, the diffusion of a defoamer is difficult and the speed of the microbubble becoming a large bubble is slow and the ability of the bubble to migrate to the surface is reduced. The foam in these coatings is quite difficult to eliminate. It is necessary to choose defoamer and defoamer to use together.
5. Painting method and construction temperature
There are many coating construction methods, such as brush coating, roller coating, dripping coating, scraping coating, spraying, and screen printing coating. Different coating methods are used, and the degree of foaming of the paint is different. Brushing, and roller coating foam is more than spraying and scraping, and high temperature than low-temperature foam, but the high-temperature foam is good elimination.